- Home
- /
- Types
- /
- Quartz Rod
- /
- Custom Fused Quartz Groove...
Customized Fused Quartz Groove Rod for Optical Fiber Laser and High Temperature Applications -TOQUARTZ®
Each fused quartz groove rod delivers exceptional thermal stability, optical transparency, and corrosion resistance for demanding industrial environments.
Features of Fused Quartz Groove Rod
Optical Clarity & Transmission
With light transmission exceeding 90% across the 200-2500nm spectrum, our fused quartz rods deliver exceptional optical performance for UV, visible, and IR applications. The material's homogeneity ensures consistent optical properties throughout the component.
Precision Machined Grooves
TOQUARTZ®'s manufacturing capabilities enable precise groove dimensions with tolerances down to ±0.05mm. This precision is critical for optical fiber positioning, component alignment, and applications requiring exact dimensional control.
Mechanical Strength
With tensile strength of 4.8×10⁷ Pa and compressive strength exceeding 1.1×10⁹ Pa, our quartz rods provide robust structural support even in challenging mechanical environments. The material's hardness (5.5-6.5 Mohs) ensures excellent wear resistance.
Surface Quality
TOQUARTZ® maintain strict surface quality standards (60/40 scratch-dig) with options for polished, ground, or custom-textured finishes. Our manufacturing process eliminates bubbles, inclusions, and defects that could compromise optical or mechanical performance.
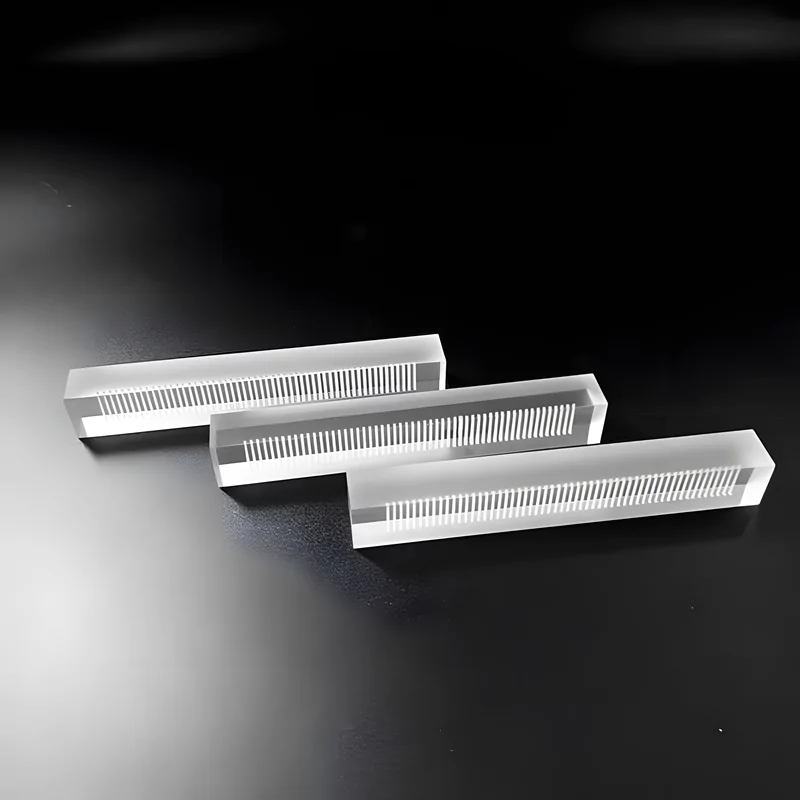
- Thermal Stability: 1100°C continuous, 1450°C short-term
- Precision Machined Grooves (±0.05mm)
- Custom Dimensions Per Drawing
Technical Specifications of Fused Quartz Groove Bar
Physical Properties
Material | 99.99% Pure Fused Quartz (SiO₂) |
Density | 2.2×10³ kg/m³ |
Hardness | 5.5 – 6.5 Mohs’ Scale (570 KHN 100) |
Tensile Strength | 4.8×10⁷ Pa (7,000 psi) |
Compressive Strength | Greater than 1.1×10⁹ Pa (160,000 psi) |
Bulk Modulus | 3.7×10¹⁰ Pa (5.3×10⁶ psi) |
Rigidity Modulus | 3.1×10¹⁰ Pa (4.5×10⁶ psi) |
Thermal Properties
Softening Point | 1730°C |
Annealing Point | 1215°C |
Continuous Working Temperature | 1100°C |
Short-term Maximum Temperature | 1450°C |
Thermal Expansion Coefficient | 5.5×10⁻⁷ /°C (20-1000°C) |
Thermal Conductivity | 1.4 W/m·K (20°C) |
Optical Properties
Transmission Range | 200-2500 nm |
UV Transmission (10mm thickness) | >80% at 200nm, >90% at 220nm |
Visible Light Transmission | >93% (400-700nm) |
Refractive Index | 1.458 (589.3nm at 20°C) |
Surface Quality | 60/40 scratch-dig standard (higher available) |
TOQUARTZ® Solving Critical Challenges with Fused Quartz Groove Rods
High-Precision Optical Fiber Support with Quartz Groove Rods
Key Advantages
-
Zero deformation at 1400°C
TOQUARTZ® groove rods maintain dimensional stability with <0.01% linear expansion at 1400°C. -
±0.05mm groove tolerance across 300mm length
Precision CNC machining ensures groove width/depth consistency within ±0.05mm over full rod length. -
OH content <10ppm for fiber-grade purity
Low hydroxyl content prevents bubble formation and optical contamination during fiber drawing.
TOQUARTZ® solution
A Japanese optical fiber manufacturer required 280mm long quartz groove rods with 0.8mm wide grooves, ±0.05mm tolerance, and thermal stability at 1350°C. Local suppliers failed to meet groove uniformity, causing fiber misalignment and 6% yield loss.
TOQUARTZ® delivered rods with <±0.03mm groove deviation and zero warping after 20 thermal cycles, restoring yield to 99.2% and reducing scrap cost by $18,000/month.
Laser Equipment Component Support Using Fused Quartz Groove Rods
Key Advantages
-
Thermal expansion coefficient 5.5×10⁻⁷/°C
Ensures <0.05mm dimensional shift over 100mm length at 1000°C, critical for laser cavity alignment. -
Outgassing rate <0.01% at 800°C
Ultra-low impurity quartz prevents optical contamination in vacuum or sealed laser environments. -
Surface flatness <10μm over 150mm
Machined surfaces maintain optical alignment accuracy in high-power laser beam paths.
TOQUARTZ® solution
A US-based laser optics integrator faced beam misalignment due to 0.12mm thermal drift in alumina supports. They required quartz rods with <0.05mm expansion at 1000°C and no outgassing.
TOQUARTZ® supplied rods with verified 5.5×10⁻⁷/°C expansion and <0.01% outgassing, reducing beam deviation to <0.02mm and improving system uptime by 17%.
Laboratory Equipment Using High-Purity Fused Silica Groove Rod
Key Advantages
-
Acid resistance: HF, HCl, H₂SO₄ stable at 1000°C
TOQUARTZ® quartz bars resist >95% of strong acids at high temperatures without surface degradation. -
Dimensional stability ±0.02mm after 10 thermal cycles
Maintains critical sample positioning accuracy in repeated heating/cooling experiments. -
Spectral transmission >90% from 200–2500nm
Enables accurate UV-VIS-IR spectroscopic analysis without signal distortion.
TOQUARTZ® solution
A German materials lab used aluminosilicate supports in a 1200°C acid vapor chamber, which degraded after 3 weeks. They needed quartz bars with acid resistance and dimensional stability.
TOQUARTZ® delivered bars with <0.02mm deformation after 10 cycles and no surface pitting after 72h HF exposure, extending part life from 3 weeks to 4 months and reducing replacement frequency by 85%.
TOQUARTZ® Customization Services for Fused Quartz Glass Groove Rod
Customization Options
TOQUARTZ® offers a wide range of customization options for fused quartz groove rods, tailored to meet the dimensional, thermal, and optical requirements of industrial and scientific applications.
- Groove Width: 0.3mm–10mm(±0.02mm tolerance available)
- Groove Depth: 0.3mm–20mm(±0.03mm tolerance)
- Rod Length: 10mm–300mm(longer available upon request)
- Groove Count & Pattern: Single/multi-groove, parallel, stepped, V-groove, U-groove
- Surface Finish: Polished (Ra < 0.05μm), Ground, Fire-polished
- Material Grade: Standard fused quartz / Low-OH / UV-grade / IR-grade
- Thermal Stability: Up to 1450°C short-term, 1100°C continuous
- Packaging: Cleanroom-grade, anti-static, foam-inserted, vacuum-sealed
Customization Process
-
Step 1: Submit Drawing or Requirements
Provide your technical drawings or detailed specifications for Fused Quartz Groove Rods, including groove width, depth, rod length, tolerance, and required quartz grade. -
Step 2: Engineering Review & Feasibility Check
Our engineers review your Fused Quartz Groove Rods design within 24 hours, assess manufacturability, and offer optimization suggestions to improve performance or reduce cost. -
Step 3: Quotation & Lead Time Confirmation
You will receive a formal quotation for your Fused Quartz Groove Rods, including unit pricing, tooling charges (if applicable), and estimated lead time—typically 10–15 working days. -
Step 4: Prototype (Optional)
For complex or high-precision Fused Quartz Groove Rods, we offer 1–3 pcs prototype production within 7 days to validate groove geometry, surface finish, and dimensional accuracy. -
Step 5: Mass Production & QC
We begin batch production of your Fused Quartz Groove Rods with 100% dimensional inspection, groove profile verification, and surface quality checks to ensure consistency and compliance. - Step 6: Secure Packaging & Global Shipping Each Fused Quartz Groove Rod is individually protected using custom foam or vacuum-sealed packaging, then shipped via DHL, FedEx, UPS, or sea freight based on your location and urgency.
· Our in-house engineers provide drawing assistance and feasibility review within 24 hours
· We offer rapid prototyping and short lead times (as fast as 7 days for custom rods)
· All custom fused quartz groove rods undergo 100% dimensional and visual inspection before shipment
This level of flexibility and responsiveness is rarely available from large-scale quartz manufacturers. TOQUARTZ is built to serve B2B clients who need precision, speed, and technical support—not just standard catalog parts.
Usage Guide of Fused Quartz Groove Bar
Handling & Storage
- Wear powder-free gloves when handling to prevent surface contamination
- Store in clean, dry conditions away from potential impacts
- Avoid sudden temperature changes that could cause thermal shock
- Keep in original packaging until ready for use
Installation
- Ensure mounting surfaces are clean and free of debris
- Use quartz-compatible mounting methods (avoid metal clamps)
- Allow for thermal expansion when mounting in high-temperature applications
- For optical applications, verify alignment before final installation
Maintenance & Cleaning
- Clean with acetone, methanol, or specialized optical cleaners
- Use lint-free wipes or optical-grade cloths for wiping
- Inspect regularly for surface contamination in optical applications
- Avoid abrasive cleaners that could damage optical surfaces
Thermal Considerations
- Heat/cool at rates below 5°C/min to prevent thermal shock
- Ensure uniform heating where possible
- Do not exceed specified maximum temperature (1450°C short-term)
- For continuous operation, maintain temperature below 1100°C
Request Engineering Consultation
Share your requirements and we'll help develop the optimal solution.
Why Partner with TOQUARTZ
Direct Factory Advantage
As a direct manufacturer, we can cut out the numerous intermediate links.
Engineering Expertise
Technical team guides clients from material selection to design optimization, translating specs into deliverables.
Flexible Manufacturing
Handling standard & custom orders via small-batch expertise and prototyping rigor to meet urgent deadlines.
Quality
Assurance
Pre-shipment 3-step validation:
1. dimensional accuracy,
2. material purity ,
3. performance thresholds
Global Supply Chain
Reliable global logistics to industrial hubs (DE/US/JP/KR priority) with trackable milestones.
Releted Products
As a specialized manufacturer with direct factory capabilities, TOQUARTZ provides both standard and custom quartz solutions with engineering support throughout the specification and implementation process.
FAQ
Q: How do quartz groove rods compare to ceramic alternatives?
A: Fused quartz groove rods offer several advantages over ceramic alternatives, including higher temperature resistance (up to 1450°C vs. 1200-1300°C for most ceramics), superior optical clarity, better thermal shock resistance, and lower thermal expansion. Quartz also provides better chemical resistance, especially to acids. However, some advanced ceramics may offer higher mechanical strength in certain applications.
Q: How should quartz groove rods be mounted in high-temperature applications?
A: For high-temperature applications, we recommend mounting quartz groove rods with non-metallic supports that accommodate thermal expansion. Ideal mounting methods include quartz-to-quartz fixtures, ceramic standoffs, or specially designed graphite holders. Metal clamps should be avoided as direct contact can cause stress points. Always allow for approximately 0.1% linear expansion when designing mounting systems for temperatures above 1000°C.
Q: Can you produce quartz groove rods with multiple different groove widths?
A: Yes,TOQUARTZ® routinely manufacture quartz groove rods with multiple groove widths, depths, and patterns on a single component. This is particularly useful for applications requiring different fiber diameters or component positioning. Our CNC machining capabilities allow for complex groove patterns including variable width grooves, intersecting channels, and stepped designs. Please provide a detailed drawing for quote and feasibility assessment.
Q: What methods do you use to cut quartz rods to custom lengths?
A: We use precision diamond cutting techniques to cut quartz rods to custom lengths. Depending on the thickness and precision requirements, we employ diamond saws, wire cutting, or abrasive waterjet cutting. For ultra-precise end faces, we can perform additional surface grinding or polishing to achieve flatness within a few microns. All cutting is performed under controlled conditions to prevent chipping or cracking.
Q: How do quartz rods perform in radiation environments?
A: Fused quartz exhibits good radiation resistance compared to many materials, though prolonged exposure can cause color centers that affect optical transmission. For radiation environments, we offer radiation-hardened grades that maintain better transparency under exposure. These specialized materials show minimal browning and maintain structural integrity in environments up to 10⁸ rads. For specific radiation applications, please consult our technical team to select the optimal material variant.
Contact our engineering team for technical consultation and pricing. We’ll help you select the optimal specifications for your application requirements.