- Home
- /
- Applications
- /
- Semiconductor Quartz Glass
- /
- Custom Process-Integrated Quartz Acid...
Custom Process-Integrated Quartz Acid Cleaning Tank for Semiconductor & PV Applications -TOQUARTZ®
Engineered for semiconductor wafer cleaning, photovoltaic cell etching, and laboratory chemical processing applications requiring exceptional corrosion resistance to HF, HCl, and HNO₃.
Features of Quartz Acid Cleaning Tank
Ultra High Purity
99.99% SiO₂ purity ensures minimal contamination in critical semiconductor processes. Strict quality control and cleanroom processing minimize impurities and particulate contamination.
Chemical Resistance
Exceptional resistance to all acids including HF, HCl, HNO₃, and other aggressive chemicals used in semiconductor wet processing. No material degradation even after prolonged exposure to concentrated acids.
High Thermal Stability
Operating temperature range up to 1100°C for long-term use and 1300°C for short-term applications. Low thermal expansion coefficient (5.5×10⁻⁷/°C) ensures dimensional stability during temperature fluctuations.
Optical Transparency
Excellent optical transparency (≥93% transmission) allows process monitoring and visual inspection during operation. Enables integration with optical sensors for process control and automation.
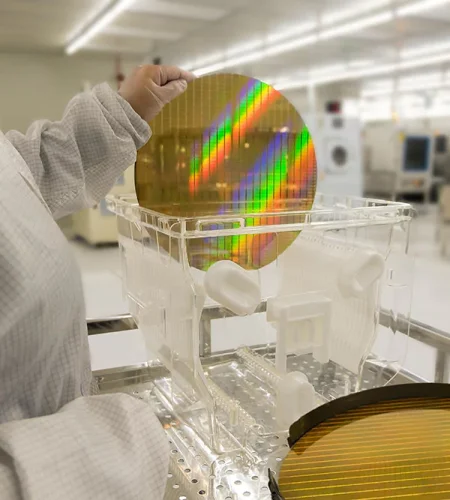
-
Ultra-low ionic contamination
release
-
Stable SiO₂ matrix under thermal-acid
cycling
-
Visual clarity for
in-situ reaction monitoring
Technical Specifications of Quartz Chemical Cleaning Tank
Technical Specifications of Quartz Glass Acid Cleaning Tank
Property | Value |
Material Composition | High purity quartz (≥99.99% SiO₂) |
Density | 2.2 g/cm³ |
Flexural Strength | 48 MPa |
Elastic Modulus | 72 GPa |
Poisson’s Ratio | 0.14-0.17 |
Compressive Strength | 1100 MPa |
Bending Strength | 67 MPa |
Mohs Hardness | 5.5-6.5 |
Maximum Working Temperature (Long-term) | 1100°C |
Maximum Working Temperature (Short-term) | 1300°C |
Thermal Conductivity | 1.4 W/m·K |
Refractive Index | 1.4585 |
Thermal Expansion Coefficient | 5.5×10⁻⁷/°C |
Specific Resistance | 7×10⁷ Ω·cm |
Optical Transmission (1mm thickness, 280-780nm) | ≥93% |
Customized Dimensions of Fused Quartz Acid Cleaning Tank
TOQUARTZ® can accommodate custom specifications based on client requirements. Contact our engineering team for detailed dimensional specifications and custom sizing options.
Solving Critical Challenges with TOQUARTZ® Quartz Acid Bath Container
Quartz Acid Cleaning Tanks for Semiconductor Wafer Processing
Key Advantages
-
Ultra-low ionic contamination release
TOQUARTZ® quartz tanks release <0.1 ppb of Na⁺, K⁺, and Al³⁺ ions after 72h HF/HCl exposure at 80°C. -
No surface degradation under mixed acid exposure
Surface roughness (Ra) remains <0.02μm after 96h in HNO₃/HF/HCl mixture at 100°C. -
Stable SiO₂ matrix under thermal-acid cycling
No microcrack propagation observed after 50 cycles of 100°C acid immersion and ambient cooling.
TOQUARTZ® solution
A Japanese 300mm wafer fab reported metal ion contamination (>0.5 ppb Al³⁺) from local quartz tanks after 48h HF/HCl use, leading to 3.2% wafer yield loss.
TOQUARTZ® supplied acid cleaning tanks with verified <0.1 ppb ion leaching (SGS test), reducing wafer surface contamination by 87% and restoring yield to 99.1% within 2 weeks of deployment.
Quartz Chemical Cleaning Tank for PV Cell Cleaning and Texturing
Key Advantages
-
No acid-induced surface pitting after 100h
TOQUARTZ® tanks show zero visible corrosion after 100h in 10% HNO₃ at 90°C. -
Stable under alkaline texturing at 85°C
No SiO₂ flaking or discoloration after 72h in NaOH/KOH solution at 85°C. -
Maintains acid bath pH stability
pH drift <0.2 over 48h in HF/HNO₃ mix, ensuring consistent etching rate.
TOQUARTZ® solution
A German PV module line using borosilicate tanks saw acid bath pH drift >0.5 in 24h, causing uneven texturing and 5% cell efficiency drop.
TOQUARTZ® quartz tanks maintained pH stability within ±0.2 over 48h, enabling uniform etching and restoring average cell efficiency from 18.3% to 19.1% across 3 production batches.
Quartz Acid Bath Containers for Research Laboratories
Key Advantages
-
Compatible with 98% of lab-grade acids and solvents
TOQUARTZ® tanks tested stable in 30+ reagents including HF, aqua regia, and perchloric acid. -
Visual clarity for in-situ reaction monitoring
≥93% light transmission (280–780nm) enables real-time observation of colorimetric reactions. -
No detectable leaching in trace analysis
<0.05 ppb total leachables after 48h in 10% HCl at 60°C (ICP-MS verified).
TOQUARTZ® solution
A Canadian university lab conducting trace metal analysis in HF/HCl reported background Al contamination >0.3 ppb from fused silica tanks.
After switching to TOQUARTZ® acid bath containers, ICP-MS baseline dropped to <0.05 ppb, enabling accurate detection of sub-ppb analytes and improving experimental reproducibility by 92%.
TOQUARTZ® Customization Services for Quartz Glass Acid Cleaning Tank
Design Customization
- Custom dimensions with precision tolerances
- Specialized inlet/outlet configurations for process integration
- Internal partitions or chambers for multi-stage processing
- Reinforced edges or corners for enhanced structural integrity
- Custom wall thickness based on thermal or structural requirements
- Integrated mounting features for equipment compatibility
Material Specifications
- Standard high-purity quartz (99.99% SiO₂)
- Opaque quartz options for light-sensitive applications
- Surface treatments for enhanced chemical resistance
- Precision-polished surfaces for critical sealing applications
- Fire-polished edges for improved mechanical strength
- Custom material certifications for regulated industries
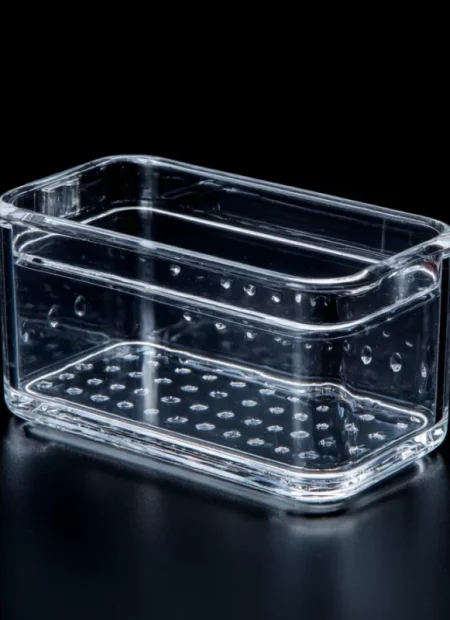
Custom Development Process
Requirement Analysis
- TOQUARTZ's technical team works with you to understand your specific process requirements, chemical environment, temperature ranges, and dimensional constraints.
Design Proposal
- We develop detailed technical drawings and specifications based on your requirements, often providing multiple design options for consideration.
Prototype Development
- For complex or novel designs, we can produce prototype units for testing and validation in your process environment before full-scale production.
Production
- Approved designs move to production with strict quality control throughout the manufacturing process to ensure dimensional accuracy and material integrity.
Quality Verification
- Each finished tank undergoes comprehensive inspection including dimensional verification, visual inspection, and material testing as required by specifications.
Usage Guidelines of Quartz Acid Cleaning Tank
Handling and Installation
- Handle with care to avoid impacts or sudden temperature changes that may cause fractures.
- Install on level, stable surfaces using appropriate supporting fixtures to distribute weight evenly.
- When mounting, use PTFE or compatible gaskets to prevent direct contact with metal surfaces.
- Allow at least 5mm clearance around the tank for thermal expansion during heated processes.
- For inlet/outlet connections, use only compatible fittings designed for quartz components.
Operating Conditions
- Do not exceed the maximum operating temperature of 1100°C for long-term use or 1300°C for short-term applications.
- Maintain temperature ramp rates below 5°C/minute to prevent thermal shock.
- For heated applications, ensure even heating distribution to avoid localized stress.
- When using with alkaline solutions, avoid contact with potassium or sodium compounds at high temperatures, which can significantly reduce performance.
- For optimum seal integrity in wet processing applications, verify that all connection points maintain specified tolerances.
Maintenance and Cleaning
- After use, thoroughly rinse with deionized water to remove chemical residues.
- For persistent contaminants, use appropriate solvents followed by ultrasonic cleaning in deionized water.
- Inspect regularly for microcracks or surface degradation, particularly at fluid connection points.
- Store in clean, dust-free environments to maintain surface integrity and prevent contamination.
- For long-term storage, cover openings with clean PTFE or polyethylene materials.
Need Technical Assistance with Quartz Acid Cleaning Tanks?
Why Partner with TOQUARTZ
Direct Factory Advantage
As a direct manufacturer, we can cut out the numerous intermediate links.
Engineering Expertise
Technical team guides clients from material selection to design optimization, translating specs into deliverables.
Flexible Manufacturing
Handling standard & custom orders via small-batch expertise and prototyping rigor to meet urgent deadlines.
Quality
Assurance
Pre-shipment 3-step validation:
1. dimensional accuracy,
2. material purity ,
3. performance thresholds
Global Supply Chain
Reliable global logistics to industrial hubs (DE/US/JP/KR priority) with trackable milestones.
Releted Products
As a specialized manufacturer with direct factory capabilities, TOQUARTZ provides both standard and custom quartz solutions with engineering support throughout the specification and implementation process.
FAQ
Q: What is the maximum temperature that quartz acid cleaning tanks can withstand?
A: TOQUARTZ® quartz acid cleaning tanks can withstand temperatures up to 1100°C for continuous long-term operation and up to 1350°C for short-term applications. The thermal stability ensures dimensional consistency even during thermal cycling, with a low thermal expansion coefficient of 5.5×10⁻⁷/°C.
Q: What types of acids are compatible with your quartz tanks?
A: TOQUARTZ® quartz acid cleaning tanks are compatible with virtually all acids used in semiconductor and photovoltaic manufacturing, including hydrofluoric acid (HF), hydrochloric acid (HCl), nitric acid (HNO₃), sulfuric acid (H₂SO₄), phosphoric acid (H₃PO₄), and various acid mixtures. They maintain their structural integrity and purity even after prolonged exposure to concentrated acids at elevated temperatures.
Q: What is the purity level of the quartz material used in your acid cleaning tanks?
A: TOQUARTZ® standard quartz acid cleaning tanks are manufactured from high-purity quartz containing ≥99.99% SiO₂. This purity level ensures minimal contamination in critical semiconductor and photovoltaic processes. The material has exceptionally low levels of alkali and metallic impurities, making it ideal for applications where contamination control is crucial for process yield and performance.
Q: How should I clean and maintain quartz acid cleaning tanks to maximize service life?
A: To maximize service life of quartz acid cleaning tanks: 1) Thoroughly rinse with DI water after each use, 2) For stubborn residues, use appropriate solvents followed by ultrasonic cleaning, 3) Avoid thermal shock by maintaining ramp rates below 5°C/minute, 4) Handle carefully to prevent mechanical impact, 5) Store in clean environments with ports covered, and 6) Regularly inspect for microcracks or surface degradation. With proper maintenance, quartz tanks can provide years of reliable service in demanding semiconductor environments.
Q: How do quartz acid cleaning tanks compare to PTFE or PFA tanks for semiconductor applications?
A: While PTFE and PFA offer excellent chemical resistance, quartz acid cleaning tanks provide several distinct advantages for semiconductor applications: 1) Superior temperature resistance (up to 1100°C vs. ~260°C for fluoropolymers), 2) Better dimensional stability under thermal cycling, 3) Higher rigidity for maintaining precise geometries, 4) Greater transparency for process monitoring, and 5) Lower particle generation and outgassing. Quartz is particularly advantageous for high-temperature acid processes common in advanced semiconductor manufacturing.
Contact our engineering team for technical consultation and pricing. We’ll help you select the optimal specifications for your application requirements.