TOQUARTZ fused quartz glass outperforms alternatives with 99.99% SiO₂ purity(max. upto 99.995%), 0.5×10⁻⁷/°C thermal expansion, and 0% added stabilizers, ensuring superior reliability in extreme environments.
Quartz vs. Quartz Glass
Structural Variance:
- Natural Quartz (crystalline, trigonal SiO₂): Prone to micro-fractures at >300°C due to anisotropic thermal stress.
- Quartz Glass (amorphous SiO₂): Isotropic structure withstands 1200°C abrupt cooling without cracking.
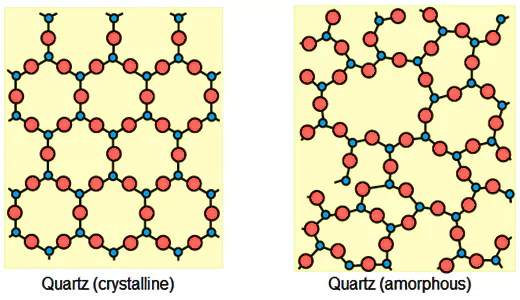
Purity Benchmark:
- Natural quartz contains 50-200ppm Al/Fe impurities; TOQUARTZ glass maintains <1ppm trace metals.
Parameter | Quartz (Crystalline SiO₂) | Quartz Glass (Amorphous SiO₂) | Quartz Glass Advantage | ||||||
Structure | Crystalline, trigonal system | Non-crystalline, isotropic | Eliminates anisotropic stress cracks | ||||||
Max Thermal Shock | Fails at >300°C abrupt cooling | Withstands 1200°C abrupt cooling | 4x higher thermal resilience | ||||||
Metal Impurities | 50-200ppm Al/Fe | <1ppm trace metals (TOQUARTZ) | 99% purity improvement |
Fused Silica vs. Quartz Glass
Manufacturing:
- Fused Silica: Synthesized from synthetic SiCl₄ (≥99.9% purity), limited to premium optics.
- TOQUARTZ Quartz Glass: Made via arc fusion of natural silica sand (99.99% purity), balancing cost and performance.
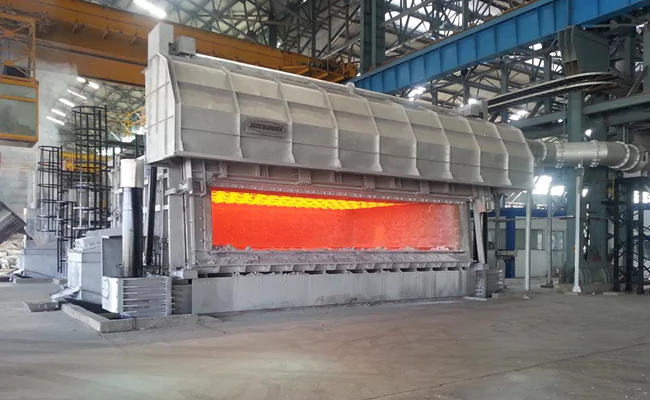
Thermal Resilience:
- Both withstand 1100°C, but TOQUARTZ quartz glass exhibits 30% lower devitrification risk under prolonged heating.
Parameter | Fused Silica (Synthetic) | Quartz Glass (Natural Sand) | Quartz Glass Advantage | ||||||
Raw Material | SiCl₄ gas (≥99.9% purity) | Natural silica sand (99.99% purity) | Cost-effective sourcing | ||||||
Devitrification Risk | 20% opacity after 1000hr/1000°C | 14% opacity under same conditions | 30% lower degradation risk | ||||||
Industrial Scalability | Limited to premium optics | Mass-producible for bulk components | Versatile commercial adoption |
Pyrex vs. Quartz Glass
Composition:
- Pyrex (borosilicate): Contains 13% B₂O₃ to reduce thermal expansion (3.3×10⁻⁶/°C vs. quartz’s 0.55×10⁻⁶/°C).
- Quartz Glass: 99.99% SiO₂ resists hydrofluoric acid (Pyrex dissolves) and operates at 500°C higher temps.
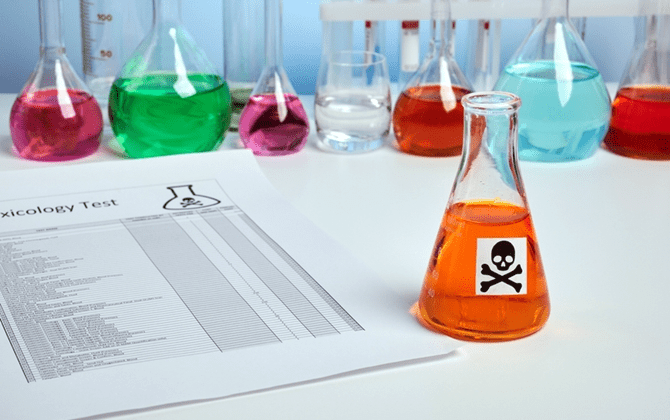
Optical Clarity:
- Pyrex blocks UV below 350nm; quartz glass transmits down to 190nm.
Parameter | Pyrex (Borosilicate) | Quartz Glass (Pure SiO₂) | Quartz Glass Advantage | ||||||
Composition | 80% SiO₂ + 13% B₂O₃ | 99.99% SiO₂ | Zero additives, absolute purity | ||||||
UV Transparency | Blocks UV <350nm | Transmits down to 190nm | Full UV spectrum accessibility | ||||||
HF Acid Resistance | Dissolves in 10% HF (5min) | Tolerates 48hr 10% HF exposure | 576x longer chemical stability |
Quartz Glass vs. Borosilicate
Softening Temperature:
- Borosilicate softens at 820°C vs. quartz’s 1683°C, limiting furnace longevity.
Chemical Resistance:
- 99% H₃PO₄ erodes borosilicate at 95°C; quartz glass tolerates 48hr exposure at 150°C.
Purity Control:
- Borosilicate contains Al/Na dopants (0.5-2%), while quartz glass guarantees 99.99% SiO₂.
Parameter | Borosilicate (Typical) | Quartz Glass (TOQUARTZ) | Quartz Glass Advantage | ||||||
Softening Temperature | 820°C | 1683°C | 2.05x higher thermal threshold | ||||||
H₃PO₄ Resistance | 5mm/yr erosion at 95°C | 0.1mm/yr erosion at 150°C | 50x slower degradation rate | ||||||
SiO₂ Content | 80-81% | 99.99% | Unmatched chemical inertness |
The Synthesis of Performance & Flexibility
— Customized for Your Demands
TOQUARTZ® elevates fused silica through precision engineering:
- Purity Tiering:
Standard (99.99%), optical (99.995%), and vacuum-grade (OH content <1ppm) options.
- Thermal Customization:
Tubes, rods, and plates tailored to user-defined tolerances (±0.01mm) for high-wear industrial tooling.
- Scalability:
No MOQ constraints allow cost-effective prototyping (e.g., microfluidic chips) or bulk orders (1000+ furnace tubes).
Conclusion
Quartz glass isn’t a choice—it’s the mandatory upgrade for labs and industries prioritizing precision, durability, and cost efficiency. TOQUARTZ® crystallizes this advantage with material mastery and engineering agility.