- Home
- /
- Types
- /
- Custom Quartz Parts
- /
- Custom Atmosphere-sealing Quartz Furnace...
Custom Atmosphere-sealing Quartz Furnace Door for Semiconductor Furnaces -TOQUARTZ®
Features of Quartz Furnace Door
Quartz furnace doors manufactured by TOQUARTZ® are precision-engineered components designed for high-temperature applications in industrial furnaces. These critical components offer a unique combination of thermal, mechanical, and chemical properties that ensure optimal performance in demanding environments.
High Temperature Resistance
Withstands operating temperatures up to 1600°C without deformation or degradation, making it ideal for high-temperature processes in semiconductor and photovoltaic manufacturing.
Thermal Shock Resistance
Excellent resistance to thermal cycling and sudden temperature changes, preventing cracking and extending operational lifespan in demanding thermal environments.
Low Thermal Expansion
With a thermal expansion coefficient of 5.5×10⁻⁷/K, quartz furnace doors maintain dimensional stability during temperature fluctuations, ensuring reliable sealing and process integrity.
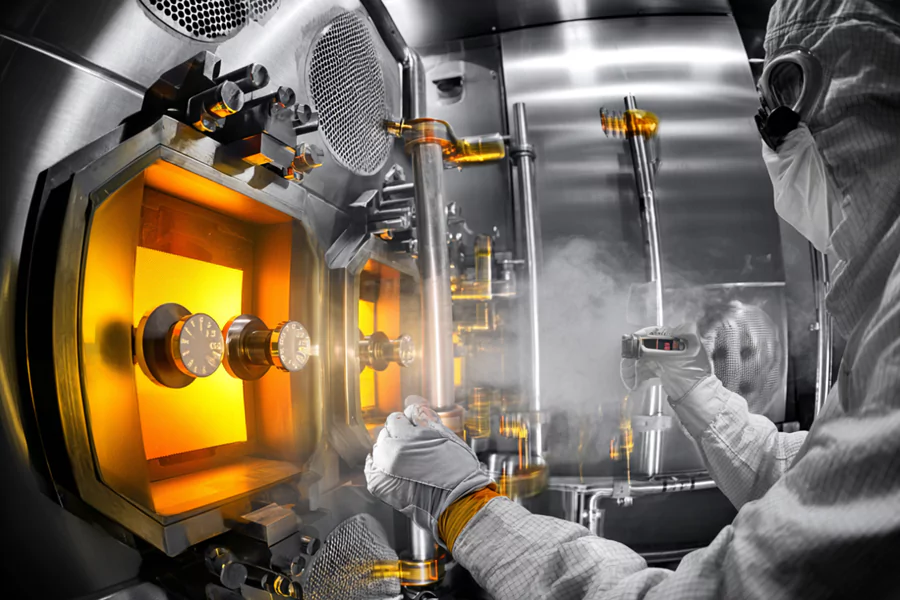
- Withstands semiconductor process corrosives
- Semiconductor-grade 99.99% SiO2
- Customizable Dimensions
Technical Specifications of Quartz Furnace Door
TOQUARTZ® quartz furnace doors are manufactured to precise specifications, ensuring optimal performance in demanding high-temperature applications. The following technical data provides detailed information about the physical, chemical, and thermal properties of our products.
Property | Value | Unit |
Material | High-purity quartz glass | – |
SiO₂ Content | ≥99.99 | % |
Maximum Working Temperature | 1600 | °C |
Thermal Expansion Coefficient | 5.5×10⁻⁷ | /K |
Thermal Conductivity | 1.3 | W/(m·K) |
Density | 2.2 | g/cm³ |
Tensile Strength | 50 | MPa |
Dimensional Tolerance | ±0.2 | mm |
Surface Finish | Fire polished | – |
Chemical Resistance | Resistant to acids, alkalis, and fluorine gases | – |
TOQUARTZ® Solving Critical Challenges with Quartz Furnace Doors
Quartz Furnace Doors in Photovoltaic Manufacturing
Key Advantages
-
Atmosphere retention accuracy within ±1.5%
Maintains dopant gas concentration stability during 950°C diffusion for uniform doping profiles. -
Doping uniformity deviation <2% across 156mm wafers
Ensures consistent sheet resistance and cell efficiency in high-throughput solar lines. -
Contamination risk reduced by 85% vs. alumina doors
High-purity quartz prevents metal ion diffusion, preserving silicon wafer integrity.
TOQUARTZ® solution
A Tier-1 solar cell manufacturer in Korea reported 2.8% yield loss due to inconsistent doping caused by gas leakage at furnace ends.
TOQUARTZ® supplied custom quartz furnace doors with optimized O-ring grooves and 99.99% SiO₂ purity. Post-installation, yield improved by 2.4%, and dopant gas usage dropped by 11%, saving over $18,000/month in material costs.
Fused Quartz Furnace Doors in Semiconductor Processing
Key Advantages
-
Particle generation <0.1 pcs/cm²/hour under 1200°C
Minimizes contamination in Class 100 cleanroom oxidation processes. -
Dimensional drift <0.05mm after 500 thermal cycles
Maintains sealing integrity during rapid annealing and oxidation cycling. -
Corrosion resistance to Cl₂ and HCl up to 1000 ppm
Ensures structural stability in aggressive semiconductor gas environments.
TOQUARTZ® solution
A U.S. semiconductor fab experienced 4 unplanned shutdowns in 2 months due to ceramic door corrosion during HCl oxidation.
TOQUARTZ® delivered quartz furnace doors with enhanced chemical resistance and dimensional stability. Downtime dropped by 92%, saving $380,000 in lost production and reducing maintenance frequency by 60%.
Quartz Glass Furnace Doors in Laboratory Research Applications
Key Advantages
-
Optical transmittance >90% at 400–800nm
Enables real-time visual monitoring of crystallization and reaction processes. -
Multi-port integration with ±0.2mm tolerance
Supports thermocouple, gas inlet, and sampling ports in compact lab setups. -
Custom turnaround time <18 days for R&D projects
Accelerates experimental timelines with rapid prototyping and delivery.
TOQUARTZ® solution
A Japanese university lab required a quartz furnace door with dual viewports and 3 gas ports for a time-sensitive crystal growth study. Standard suppliers quoted 6–8 weeks.
TOQUARTZ® delivered a fully customized unit in 17 days. The project met its funding milestone, and the lab reported a 30% improvement in experimental throughput.
TOQUARTZ® Customization Services for Fused Silica Furnace Door
Engineering & Design
- Technical drawing conversion and optimization
- 3D modeling for complex geometries
- Material selection for specific applications
- Design consultation for optimal performance
Manufacturing Capabilities
- Custom dimensions and wall thicknesses
- Specialized sealing surface configurations
- Integration of viewports or access ports
- O-ring groove designs for specific sealing requirements
Expedited Services
- Rapid prototyping for design validation
- Small batch production for testing
- Emergency replacement manufacturing
- 24-hour shipping for stock items
Usage Guidelines of Quartz Furnace Door
Proper handling, installation, and maintenance of quartz furnace doors are essential for maximizing service life and ensuring optimal performance in high-temperature applications. Follow these guidelines to prevent damage and extend the operational lifespan of your quartz components.
Handling & Storage
- Wear clean, powder-free gloves when handling quartz furnace doors to prevent surface contamination
- Store in original packaging or on clean, padded surfaces away from potential impacts
- Maintain storage environment at controlled temperature and humidity (40-60% RH)
- Avoid exposure to hydrofluoric acid (HF) during storage
- Inspect for microcracks or damage before installation
Installation Procedure
- Clean mounting surfaces thoroughly before installation
- Use appropriate high-temperature O-rings or gaskets that are compatible with process gases
- Apply even pressure when securing - avoid overtightening which can create stress pointsApply even pressure when securing - avoid overtightening which can create stress points
- Follow recommended torque specifications for mounting hardware
- Allow adequate clearance for thermal expansion during operation
Temperature Management
- Observe maximum rated temperature (1200°C for standard quartz doors)
- Control heating rates to <100°C/hour during initial warm-up to prevent thermal shock
- Ensure temperature uniformity across the door to prevent localized stress
- Allow for gradual cooling when powering down furnace systems
- Avoid direct contact with cooling systems or heat sinks
Maintenance & Cleaning
- Inspect sealing surfaces regularly for deposits or damage
- Clean with high-purity isopropyl alcohol or acetone and lint-free wipes
- For stubborn deposits, use dilute acid solutions (except HF) followed by thorough rinsing
- Replace O-rings and gaskets according to manufacturer's schedule
- Document maintenance history to track component lifetime and performance
Replacement Indicators
- Visible microcracks or surface devitrification
- Difficulty maintaining process atmosphere
- Declining process performance or yield
- Increased gas consumption or pressure fluctuations
Need Engineering Support for Your Furnace Components?
and design optimization to ensure optimal performance in your specific environment.
Why Partner with TOQUARTZ
Direct Factory Advantage
As a direct manufacturer, we can cut out the numerous intermediate links.
Engineering Expertise
Technical team guides clients from material selection to design optimization, translating specs into deliverables.
Flexible Manufacturing
Handling standard & custom orders via small-batch expertise and prototyping rigor to meet urgent deadlines.
Quality
Assurance
Pre-shipment 3-step validation:
1. dimensional accuracy,
2. material purity ,
3. performance thresholds
Global Supply Chain
Reliable global logistics to industrial hubs (DE/US/JP/KR priority) with trackable milestones.
Releted Products
As a specialized manufacturer with direct factory capabilities, TOQUARTZ provides both standard and custom quartz solutions with engineering support throughout the specification and implementation process.
FAQ
Q: What is a quartz furnace door used for?
A: Quartz furnace doors are used to seal the ends of high-temperature furnaces while maintaining stable internal temperature and atmosphere conditions. They’re critical components in semiconductor manufacturing, photovoltaic production, and laboratory research where process integrity and contamination control are essential. The doors help maintain precise gas composition and prevent heat loss while allowing process monitoring in some configurations.
Q: How to replace a quartz furnace door in a diffusion furnace?
A: To replace a quartz furnace door in a diffusion furnace:
1. Ensure the furnace has cooled completely to prevent thermal shock
2. Disconnect any gas lines or monitoring equipment attached to the door
3. Remove mounting hardware while supporting the door to prevent dropping
4. Carefully extract the old door without contacting heating elements
5. Clean the mounting surface thoroughly
6. Inspect and replace O-rings or gaskets
7. Install the new quartz door using appropriate mounting hardware
8. Tighten fasteners in a cross-pattern to ensure even pressure
9. Reconnect gas lines and monitoring equipment
10. Test for leaks using an appropriate method for your process gases
Q: Can quartz furnace doors withstand high temperature cycling?
A: Yes, quartz furnace doors are specifically designed to withstand high-temperature cycling. Their low thermal expansion coefficient (5.5×10⁻⁷/K) makes them highly resistant to thermal shock and dimensional changes during heating and cooling cycles. Proper quartz doors can typically withstand thousands of thermal cycles between room temperature and operating temperatures up to 1600°C, provided that heating and cooling rates are controlled (generally recommended at <100°C/hour during initial heating and final cooling phases). For optimal cycling performance, uniform heating/cooling and proper mounting to allow for minimal thermal expansion are essential.
Q: What is the maximum temperature for a quartz furnace door?
A: Standard high-purity quartz furnace doors can withstand continuous operating temperatures up to 1600°C. The practical maximum temperature depends on several factors including:
1. Duration of exposure (continuous vs. intermittent)
2. Rate of temperature change (thermal shock resistance)
3. Mechanical stress during mounting
4. Presence of alkali contaminants (which can lower softening point)
At temperatures approaching 1600°C, quartz begins to devitrify over time, forming crystalline structures that can compromise mechanical integrity. For applications requiring temperatures above 1600°C, specialized formulations or alternative materials may be required.
Q: How to custom order a quartz furnace door for a tube furnace?
A: To custom order a quartz furnace door for a tube furnace, provide the following information:
1. Outer diameter and wall thickness of your furnace tube
2. Required sealing method (O-ring, flanged connection, etc.)
3. Any ports needed (gas inlets/outlets, thermocouple access, etc.)
4. Temperature range and cycling requirements
5. Process atmosphere composition (especially if corrosive gases are present)
6. Technical drawings or photographs of current setup (if available)
7. Application description to help optimize the design
TOQUARTZ can develop a custom design based on your requirements, provide technical drawings for approval, and manufacture to precise specifications with typical lead times of 2-3 weeks for custom designs.
Contact our engineering team for technical consultation and pricing. We’ll help you select the optimal specifications for your application requirements.