- Home
- /
- Types
- /
- Custom Quartz Parts
- /
- Custom Contamination-Free Quartz Reaction...
Custom Contamination-Free Quartz Reaction Vessel for Semiconductor Processing -TOQUARTZ®
TOQUARTZ® manufactures quartz reactors with up to 99.995% SiO₂ purity for applications where material integrity is critical.
Features of Quartz Reaction Vessel
TOQUARTZ® industrial-grade quartz reaction vessels are engineered for exceptional performance in demanding laboratory and manufacturing environments, offering superior material properties compared to standard glass or ceramic alternatives.
High Material Purity
Manufactured with max. up to 99.995% SiO₂ purity, minimizing contamination risks in sensitive research and manufacturing processes.
Mechanical Strength
Features fracture modulus exceeding 350MPa, providing durability in demanding industrial and research environments.
High Temperature Resistance
Withstands continuous operation at temperatures up to 1200°C without deformation or degradation, ideal for high-temperature chemical reactions.
Chemical Resistance
Exhibits exceptional stability against acids, bases, molten salts, and fluorinated gases, preventing contamination in sensitive chemical processes.
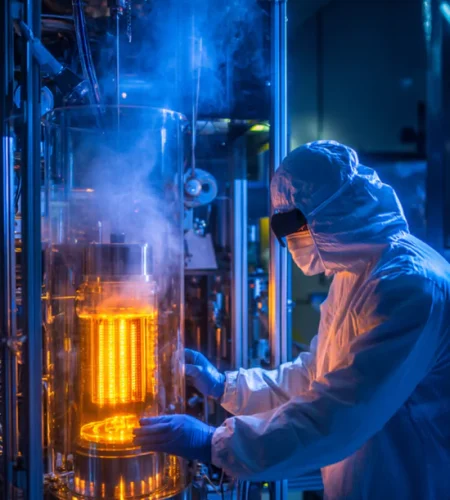
-
Max. up to 99.995%
SiO₂ Purity
-
Low metallic
impurity content
-
Custom geometries
available
Technical Specifications & Dimensions of Quartz Reaction Vessel
TOQUARTZ® quartz reaction vessels are manufactured to precise specifications that exceed industry standards, ensuring optimal performance in demanding applications.
Technical Specifications of Fused Quartz Reaction Vessel
Physical Properties
Property | Value | Testing Method |
Maximum Working Temperature | 1200°C | ASTM C1055 |
Thermal Expansion Coefficient | 0.5 × 10⁻⁶/K | ASTM E228 |
Thermal Conductivity | 120-160 W/m·K | ASTM C177 |
Density | 2.2 g/cm³ | ASTM C693 |
Fracture Modulus | ≥350 MPa | ASTM C1161 |
Chemical Properties
Property | Value | Testing Method |
SiO₂ Purity | 99.995% | ICP-MS |
Acid Resistance (HF excluded) | Excellent | ASTM C724 |
Alkali Resistance (≤80°C) | Very Good | ASTM C225 |
OH Content | ≤20 ppm | IR Spectroscopy |
Metal Impurities (Total) | ≤50 ppm | ICP-MS |
Optical Properties
Property | Value | Testing Method |
Refractive Index (589.3nm) | 1.4585 | ASTM D542 |
UV Transmission (254nm) | ≥80% (2mm thickness) | Spectrophotometry |
IR Transmission (2.7μm) | ≥85% (2mm thickness) | Spectrophotometry |
Dimensional Specifications of Quartz Glass Reaction Chamber
Standard Size Ranges:
- Inner Diameter: 20mm - 500mm
- Wall Thickness: 2mm - 10mm
- Length: Up to 1500mm
- Volume: 10ml - 20L
Manufacturing Precision:
- Standard Tolerance: ±0.2mm
- Precision Tolerance (select applications): ±0.1mm
- Surface Finish: Ground or Polished
- Custom Flange/Connection Compatibility: Available
TOQUARTZ® Solving Challenges with Quartz Reaction Vessels
Quartz Reaction Vessels for Laboratory Research
Key Advantages
-
Ultra-low thermal drift during extended heating
Maintains dimensional stability within ±0.1mm after 8-hour exposure at 1100°C. -
Verified impurity leaching below 0.5 ppm
ICP-MS tests show <0.5 ppm total leachables after 6-hour acid reflux at 95°C. -
Stable performance across 100+ thermal cycles
No visible devitrification or microcracks after 120 thermal cycles between 25°C and 1000°C.
TOQUARTZ® solution
A German university lab conducting 72-hour high-temp synthesis (1050°C) reported borosilicate vessel deformation after 18 hours. TOQUARTZ supplied custom quartz vessels with ±0.1mm tolerance and 99.995% SiO₂ purity. After 3 months of continuous use, no dimensional drift or contamination was detected, improving experiment repeatability by 27%.
Fused Quartz Reaction Vessels for Chemical Synthesis
Key Advantages
-
Acid vapor resistance validated for 200+ hours
No surface degradation after 240-hour exposure to HCl/HNO₃ vapor at 90°C. -
Metal ion leaching <0.2 ppm in oxidizing media
Total Fe, Al, Na ions remained below 0.2 ppm after 5-hour reflux in mixed oxidants. -
Structural integrity under corrosive gas flow
No wall thinning or cracking after 100 cycles of Cl₂ gas flow at 600°C.
TOQUARTZ® solution
A Polish catalyst manufacturer faced 14% batch rejection due to vessel-sourced Fe/Al contamination. TOQUARTZ delivered custom quartz reactors with <0.2 ppm leachables and acid vapor resistance. Within 2 months, rejection rate dropped to 2.1%, and vessel lifespan extended from 3 to 9 months, saving approx. €18,000 annually.
Quartz Glass Quartz Reaction Vessels for High-Temperature Industrial Processes
Key Advantages
-
Dimensional tolerance maintained at 1200°C
±0.15mm tolerance held after 6-hour exposure to 1200°C in CVD furnace. -
No devitrification after 150 thermal cycles
Surface remained optically clear after 150 cycles between 25°C and 1150°C. -
Surface roughness Ra < 0.4μm for optical-grade use
Polished inner walls achieved Ra 0.38μm, suitable for photochemical precision.
TOQUARTZ® solution
A Japanese photonics firm required reaction vessels for UV-assisted CVD at 1150°C. Local suppliers offered 8-week lead time with ±0.3mm tolerance. TOQUARTZ delivered within 21 days, achieving ±0.15mm tolerance and Ra 0.38μm surface finish. This enabled 96% first-pass yield and reduced calibration downtime by 40%.
TOQUARTZ® Customization Services for Fused Silica Reaction Vessel
Custom Design Capabilities
-
Complex Geometries:
Custom vessel shapes including multi-chamber designs, specialized inlets/outlets, and internal structures optimized for your specific reaction processes. -
Connection Integration:
Custom flange designs, ground joint fittings, or proprietary connection systems compatible with your existing equipment. -
Precision Requirements:
Tighter tolerance specifications (±0.1mm) available for critical dimensions where standard tolerances (±0.2mm) are insufficient. -
Surface Treatments:
Specialized finishes including precision polishing, fire polishing, or custom etch patterns for specific reaction environments.
Engineering Support
TOQUARTZ® dedicated team of quartz engineering specialists works directly with your technical team to optimize designs for manufacturability, performance, and cost-effectiveness.
We offer:
- Design optimization for quartz manufacturing processes
- Material selection guidance for specific application requirements
- Design drawing assistance from sketches or verbal descriptions
- Prototype development and performance validation
2. Collaborative design development and quotation
3. Precision manufacturing with rigorous quality control
4. Secure packaging and prompt international shipping
Usage Guidelines of Quartz Reaction Vessel
Proper handling, operation, and maintenance of quartz reaction vessels are essential for maximizing performance and service life in laboratory and industrial applications.
Handling Recommendations
-
Avoid Thermal Shock:
Temperature changes should not exceed 200°C/minute to prevent stress fractures. Allow gradual heating and cooling cycles. -
Support Distribution:
Ensure even mechanical support during installation. Concentrated stress points may lead to failure under thermal cycling. -
Connection Interfaces:
For flanged vessels, use appropriate gasket materials rated for your temperature range. Over-tightening can crack quartz flanges.
Cleaning & Maintenance
-
Standard Cleaning:
For most residues, use dilute laboratory-grade detergents followed by thorough rinsing with deionized water. Finish with analytical-grade acetone or isopropanol. -
Heavy Contamination:
For carbon deposits, a controlled oxidation process at 800-1000°C can remove organic residues. Always follow with standard cleaning. -
Inspection Routine:
Regularly inspect for microcracks, devitrification (cloudy appearance), or surface degradation. Perform visual inspections after each thermal cycle above 1000°C.
Operation Best Practices
-
Temperature Monitoring:
Install temperature monitoring at multiple points to ensure even heating and prevent localized hot spots. -
Pressure Management:
Do not exceed specified pressure ratings. For high-pressure applications, use specially designed vessels with appropriate wall thickness. -
Chemical Compatibility:
While quartz is highly resistant to most chemicals, hydrofluoric acid (HF) will attack quartz. Consult our technical team for specialized applications.
Storage Recommendations
-
Clean Environment:
Store in dust-free, controlled environment. Avoid contact with materials that could cause scratches or impacts. -
Support Considerations:
Store with appropriate cushioning on non-abrasive surfaces. Avoid point-loading on large vessels. -
Pre-Use Inspection:
After prolonged storage, inspect sealing surfaces and test with low-temperature run before high-temperature application.
Need Assistance with Your Quartz Reaction Vessel Requirements?
Why Partner with TOQUARTZ
Direct Factory Advantage
As a direct manufacturer, we can cut out the numerous intermediate links.
Engineering Expertise
Technical team guides clients from material selection to design optimization, translating specs into deliverables.
Flexible Manufacturing
Handling standard & custom orders via small-batch expertise and prototyping rigor to meet urgent deadlines.
Quality
Assurance
Pre-shipment 3-step validation:
1. dimensional accuracy,
2. material purity ,
3. performance thresholds
Global Supply Chain
Reliable global logistics to industrial hubs (DE/US/JP/KR priority) with trackable milestones.
Releted Products
As a specialized manufacturer with direct factory capabilities, TOQUARTZ provides both standard and custom quartz solutions with engineering support throughout the specification and implementation process.
FAQ
Q: What is a quartz reaction vessel used for?
A: Quartz reaction vessels are used for high-temperature chemical reactions, material synthesis, photochemical processes, and specialized laboratory applications where exceptional temperature resistance, chemical inertness, and purity are required. They’re commonly used in research laboratories, material science facilities, semiconductor manufacturing, and chemical synthesis operations where standard glass or metal vessels would degrade or contaminate the process.
Q: Can quartz reaction vessels withstand high temperatures?
A: Yes, quartz reaction vessels can withstand continuous operation at temperatures up to 1200°C without deformation or degradation. The softening point of high-purity quartz is approximately 1683°C, though practical use is limited to lower temperatures to maintain dimensional stability and avoid devitrification. For comparison, borosilicate glass typically has a maximum working temperature of around 500°C before softening begins.
Q: Are quartz reaction vessels chemically resistant?
A: Quartz reaction vessels offer exceptional chemical resistance to most substances, including:
· Strong acids (except hydrofluoric acid)
· Weak to moderate bases at temperatures below 80°C
· Organic solvents and compounds
· Halogens and halogenated compounds
· Most molten salts
· Fluorinated gases at elevated temperatures
The primary chemical limitation is hydrofluoric acid (HF) and hot concentrated alkaline solutions, which will attack the SiO₂ structure. For these specific applications, alternative materials should be considered.
Q: What are the advantages of quartz over glass in reaction vessels?
A: Quartz offers several key advantages over standard borosilicate glass for reaction vessels:
· Higher temperature resistance (1200°C vs. ~500°C for borosilicate)
· Lower thermal expansion coefficient for better thermal shock resistance
· Superior chemical resistance, especially to strong acids
· Higher purity with minimal leaching of elements into reactions
· Better UV and IR transmission properties
· Higher mechanical strength and durability in harsh conditions
Q: Where to buy custom quartz reaction vessels?
A: TOQUARTZ specializes in manufacturing custom quartz reaction vessels for laboratory, research, and industrial applications. As a direct factory supplier, we offer:
· Custom design and engineering support
· High-purity quartz (up to 99.995% SiO₂)
· Precision tolerances (standard ±0.2mm, precision ±0.1mm)
· Small batch capabilities (minimum orders as low as 1-10 pieces)
· Rapid delivery timelines (2-4 weeks for custom designs)
· Complete technical documentation and support
You can request a custom quote through our website or by contacting our technical sales team at info@toquartz.com.
Contact our engineering team for technical consultation and pricing. We’ll help you select the optimal specifications for your application requirements.