- Home
- /
- Types
- /
- Custom Quartz Parts
- /
- Custom Ultra Pure Quartz...
Custom Ultra Pure Quartz Ingot for Semiconductor & Solar Applications -TOQUARTZ®
Our quartz ingots serve as primary materials for manufacturing semiconductor components, photovoltaic cells, optical elements, and specialized laboratory equipment requiring high-temperature stability and chemical resistance.
Features of Quartz Ingot
TOQUARTZ® high purity quartz ingots deliver exceptional performance for demanding industrial applications where material integrity and thermal stability are critical requirements.
High Purity Composition
TOQUARTZ® quartz ingots achieve 99.995% SiO₂ purity with minimal trace elements, making them suitable for semiconductor and optical applications.
- Trace element content (ppm): Al: 20, Fe: 0.4, Na: 1.5, K: 1
- OH content: 120-260 ppm
- No black spots or visible impurities
Mechanical & Chemical Properties
TOQUARTZ® quartz ingots offer exceptional mechanical strength and chemical resistance for industrial applications.
- High fracture modulus: up to 350MPa
- Resistant to acids, alkalis, and molten salts
- Excellent electrical insulation properties
- Low friction coefficient for high flow applications
Thermal Properties
Superior thermal stability makes our quartz ingots ideal for high-temperature industrial processes and manufacturing.
- Maximum operating temperature: 1200°C
- Thermal conductivity: 120-160 W/m·K
- Thermal expansion coefficient: 5.5×10⁻⁷/K
- Excellent thermal shock resistance
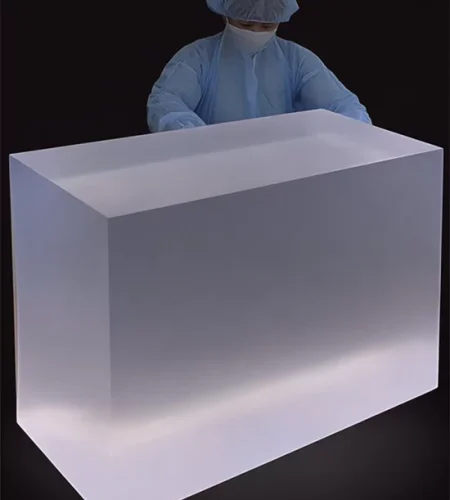
-
Up to 99.995%
SiO₂ Purity
-
Low metallic
impurity content
-
Custom geometries
available
Technical Specifications & Dimensions of Quartz Ingot
TOQUARTZ® quartz ingots are manufactured to precise specifications for various industrial applications requiring high purity silica materials.
Chemical Composition Analysis (Reference Values in PPM)
Element | Value | Element | Value | Element | Value | Element | Value |
Al (Aluminum) | 20 | Fe (Iron) | 0.4 | K (Potassium) | 1 | Li (Lithium) | 1.4 |
Cu (Copper) | 0.01 | Na (Sodium) | 1.5 | B (Boron) | 0.2 | Ca (Calcium) | 0.5 |
Mg (Magnesium) | 0.05 | P (Phosphorus) | 0.06 | Ti (Titanium) | 1.2 | OH (Hydroxyl) | 120-260 |
Size Chart of Quartz Glass Ingot
Model | Description | Dimensions |
AT-SIO-T1001 | Transparent Round Ingot | Ø150 × H600mm |
AT-SIO-T1002 | Transparent Round Ingot | Ø650 × H200mm |
AT-SIO-T1003 | Transparent Square Ingot | 450 × 450 × H200mm |
AT-SIO-T1004 | Transparent Square Plate (Polished) | 10 × 10 × ≥0.5mm |
AT-SIO-T1005 | Transparent Square Plate (Polished) | 600 × 600 × 3-5mm |
AT-SIO-T1006 | Transparent Square Plate (Rough) | Max: 400 × 3000 × 5-10mm |
AT-SIO-T1007 | Transparent Round Plate | Ø2 × ≥0.5mm |
AT-SIO-T1008 | Transparent Round Plate | Ø650 × 3-5mm |
TOQUARTZ® Solving Industry Challenges with Quartz Ingots
Quartz Ingots for Semiconductor Manufacturing
Key Advantages
-
Ultra-low metallic impurity content
Fe < 0.4 ppm and Cu < 0.01 ppm ensure minimal contamination in wafer processing. -
Dimensional stability under thermal cycling
No deformation observed after 1000+ cycles at 1100°C in diffusion furnace environments. -
OH content control for plasma compatibility
OH content maintained at 120–260 ppm to reduce microcrack formation in etching chambers.
TOQUARTZ® solution
A German wafer fab reported 8% yield loss due to metallic contamination from local quartz. After switching to TOQUARTZ® ingots with Fe < 0.4 ppm, defect rates dropped by 6.7%. Etching chamber downtime reduced by 18%, saving approx. €42,000 per quarter. The client extended the supply contract for 3 years based on performance stability.
Fused Quartz Ingots for Solar Cell Production
Key Advantages
-
Uniform thermal conductivity for crystal growth
Thermal conductivity of 130±5 W/m·K ensures stable heat transfer in CZ furnaces. -
Controlled OH content for crucible longevity
OH content of 120–260 ppm reduces devitrification during silicon melting cycles. -
Low B and P contamination for high-efficiency cells
Boron < 0.2 ppm and Phosphorus < 0.06 ppm meet Tier-1 PV cell purity standards.
TOQUARTZ® solution
A Japanese solar cell manufacturer faced 11% crucible failure rate due to devitrification. TOQUARTZ® ingots with controlled OH and low B content reduced failure to 2.5%. Cell efficiency improved by 0.3%, increasing annual output by 1.2 million units. The client reported ROI improvement of ¥6.8 million within 9 months.
Optical Grade Quartz Glass Ingots for Precision Components
Key Advantages
-
Homogeneous refractive index across entire ingot
Δn < 1×10⁻⁶ verified by interferometry ensures optical consistency in lens production. -
Bubble-free internal structure
Bubble content ≤ 0.01 pcs/cm³ meets ISO 10110-3 for high-precision optics. -
Surface roughness control for direct polishing
As-cast surface Ra < 0.8μm reduces pre-polishing time by 30% in optical workshops.
TOQUARTZ® solution
A U.S. scientific optics firm had 14% rejection rate due to refractive index variation. After adopting TOQUARTZ® optical ingots, rejection dropped to 2.1% over 3 months. Polishing time per lens reduced by 28%, saving $19,000 in labor costs per quarter. The client now uses TOQUARTZ® exclusively for all UV-grade optical components.
TOQUARTZ® Customization Services for Fused Silica Ingots
Custom Quartz Ingot Solutions
TOQUARTZ® engineering team works directly with clients to develop custom quartz ingot specifications that meet their exact requirements.
-
Dimensions:
Custom sizes from small precision components to large industrial-scale ingots -
Shapes:
Round, square, rectangular, or custom geometric configurations -
Surface finishing:
Polished, ground, or as-cast surfaces to specification -
Tolerances:
Precision dimensions to ±0.1mm for most applications -
Application-specific properties:
Optimized for semiconductor, solar, or optical requirements
Engineering Support Services
TOQUARTZ® engineering team provides comprehensive technical support throughout your project lifecycle.
- Material selection for specific applications
- Design optimization for manufacturability
- Technical drawing review and recommendations
2. Technical drawing review and manufacturing feasibility assessment
3. Prototyping and sample production for verification
4. Full production with comprehensive quality control
Usage Guidelines of Quartz Ingot
Proper handling, storage, and processing of quartz ingots ensures optimal performance and extends product lifespan.
Handling Recommendations
- Always wear clean gloves when handling quartz ingots to prevent surface contamination.
- Avoid direct contact with other materials that could scratch or contaminate the surface.
- Use appropriate lifting equipment for larger ingots to prevent damage and ensure safety.
- Inspect for any surface defects before processing to optimize material usage.
Quality Maintenance Tips
- Perform regular visual inspections for any defects before and during processing.
- Document batch numbers and maintain traceability throughout your production process.
- For critical applications, conduct spectroscopic analysis to verify material properties.
- Implement proper disposal procedures for processing waste according to local regulations.
Storage Guidelines
- Store in clean, dry conditions at stable room temperature (15-25°C).
- Keep in original packaging until ready for use to prevent contamination.
- Use dust-free cabinets for long-term storage of optical grade material.
- Avoid rapid temperature changes which may induce thermal stress.
Processing Recommendations
- Use diamond tools specifically designed for quartz processing.
- Implement controlled heating and cooling rates (≤5°C/min) to prevent thermal shock.
- Clean with ultrapure water or high-grade solvents appropriate for your application.
- For optical applications, follow standard polishing procedures using cerium oxide or similar compounds.
Need Technical Assistance with Your Quartz Ingot Requirements?
Why Partner with TOQUARTZ
Direct Factory Advantage
As a direct manufacturer, we can cut out the numerous intermediate links.
Engineering Expertise
Technical team guides clients from material selection to design optimization, translating specs into deliverables.
Flexible Manufacturing
Handling standard & custom orders via small-batch expertise and prototyping rigor to meet urgent deadlines.
Quality
Assurance
Pre-shipment 3-step validation:
1. dimensional accuracy,
2. material purity ,
3. performance thresholds
Global Supply Chain
Reliable global logistics to industrial hubs (DE/US/JP/KR priority) with trackable milestones.
Releted Products
As a specialized manufacturer with direct factory capabilities, TOQUARTZ provides both standard and custom quartz solutions with engineering support throughout the specification and implementation process.
FAQ
Q: What is the maximum purity level available for your quartz ingots?
A: TOQUARTZ® highest grade quartz ingots achieve 99.995% SiO₂ purity, suitable for semiconductor and other high-tech applications requiring minimal trace elements.
Q: What are the temperature limitations of your quartz ingots?
A: TOQUARTZ® standard quartz ingots maintain structural integrity up to 1200°C. For applications requiring higher temperature resistance, please consult with our engineering team for specialized formulations.
Q: How should quartz ingots be stored to maintain quality?
A: Store in clean, dry environments away from contaminants. For optical grade ingots, maintain dust-free storage conditions. Avoid direct contact with other materials that could cause surface scratching or contamination.
Q: Can you provide material certificates for quartz ingots?
A: Yes, we provide material certification including chemical composition analysis, dimensional verification, and visual inspection reports for all our quartz ingot products.
Q: What are the standard sizes available for quartz ingots?
A: We offer standard round ingots from 150mm to 650mm diameter and rectangular ingots up to 450×450mm. Custom dimensions are available upon request for specific project requirements.
Contact our engineering team for technical consultation and pricing. We’ll help you select the optimal specifications for your application requirements.